The reasons for the formation of fusion lines in injection molding products are multifaceted, mainly related to factors such as the characteristics of plastic materials, mold design, injection molding process parameters, and product structure. The following is a detailed introduction:
Plastic Material Characteristics
Fluidity: Different types of plastics have varying fluidities. Crystalline plastics such as polyethylene and polypropylene have good fluidity in the molten state, while non-crystalline plastics like polycarbonate and polyphenylene oxide have relatively poor fluidity. Plastics with poor fluidity have inconsistent advancing speeds of the melt front during the mold filling process, making it easy to form obvious fusion lines at the confluence points.
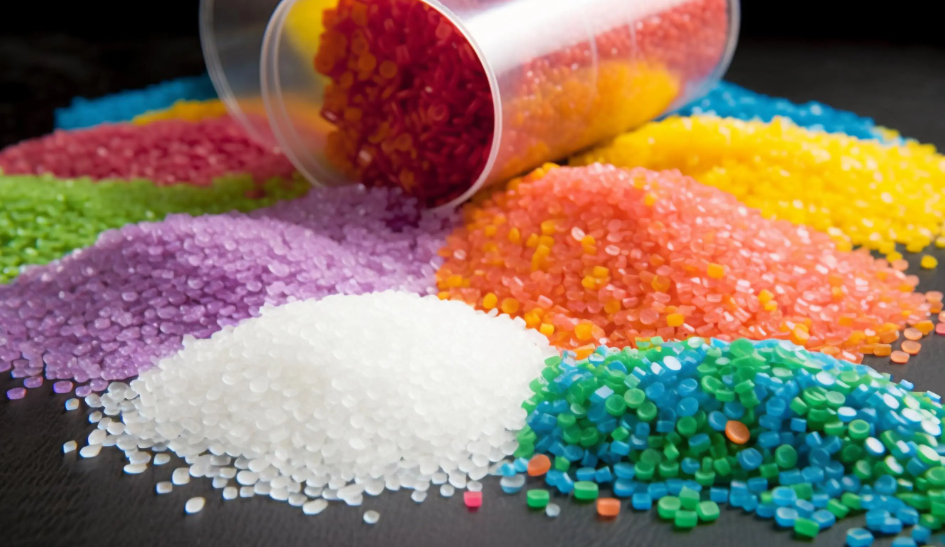
Thermal Stability: Plastics with poor thermal stability are prone to chemical reactions such as degradation and cross-linking during the high-temperature injection molding process, which changes the properties of the melt and affects its flow and fusion performance. For example, polyoxymethylene is likely to decompose at high temperatures, and the generated small molecular gases and other substances will interfere with the normal flow of the melt, promoting the formation of fusion lines.
Influence of Additives: To improve the properties of plastics, some additives such as fillers, plasticizers, and flame retardants are usually added. The addition of fillers may reduce the fluidity of the plastic, making the melt more likely to stagnate and converge during the flow process, resulting in obvious fusion lines. For example, after adding calcium carbonate filler to polypropylene, the fluidity of the melt decreases, and the problem of fusion lines may become more prominent.
Mold Design
Gate Position and Quantity: The gate position and quantity directly affect the flow path and confluence of the melt. If the gate position is not reasonable, causing the melt to flow a long distance or in a complex direction in the mold cavity, fusion lines are likely to occur. For example, when a single-point gate is used, the melt flows radially from the gate, and fusion lines are likely to form at the confluence points on the opposite sides of the melt. In the case of a multi-gate design, if the gate distribution is uneven or the gate sizes are inconsistent, it will also lead to unbalanced melt flow and the generation of fusion lines.
Runner Design: The shape, size, and roughness of the runner have an important impact on the melt flow. If the runner is too narrow or too long, it will increase the flow resistance of the melt, reduce the melt flow rate, and increase the time difference for the melt at different positions to reach the confluence point, thus aggravating the formation of fusion lines.
Ventilation System: Poor ventilation of the mold is an important factor leading to fusion lines. During the injection molding process, the air in the mold cavity, the volatile gases from the plastic, etc. need to be discharged in a timely manner. If the ventilation is poor, these gases will form an air resistance at the melt confluence point, hindering the normal fusion of the melt, weakening the bonding force at the fusion line, and making the fusion line more obvious.
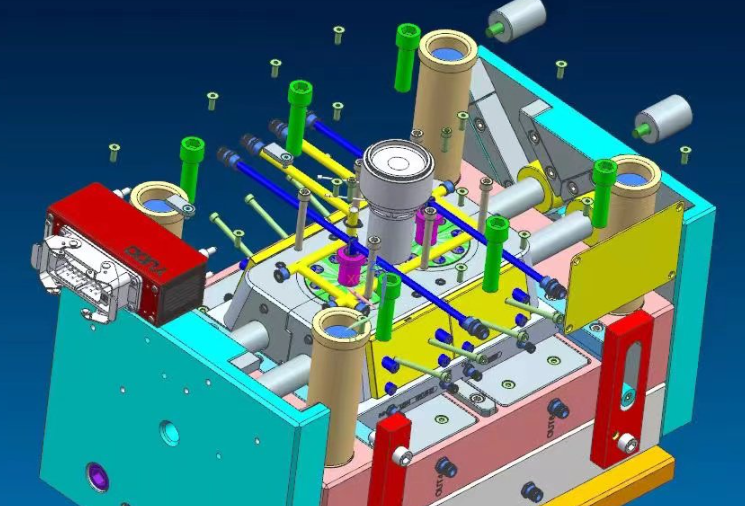
Injection Molding Process Parameters
Injection Speed: The injection speed has a significant impact on the formation of fusion lines. If the injection speed is too slow, the advancing speed of the melt front in the cavity is inconsistent. The melt that enters the cavity first cools down relatively quickly, and there is a large temperature difference between it and the later-entering melt. It is difficult to fully fuse when they meet, and obvious fusion lines are likely to form.
Injection Pressure: Insufficient injection pressure cannot provide enough power for the melt to flow quickly and evenly in the cavity. The melt is prone to stagnation and convergence during the flow process, resulting in fusion lines.
Mold Temperature: If the mold temperature is too low, the melt cools down too quickly on the cavity surface, and the fluidity of the melt decreases rapidly. It is difficult to fully fuse at the confluence point, forming fusion lines. Moreover, uneven mold temperature will also cause different cooling rates of the melt at different positions, further aggravating the formation of fusion lines.
Holding Pressure Time and Pressure: If the holding pressure time is too short or the holding pressure is insufficient, during the cooling and shrinkage process, the melt at the fusion line does not receive enough replenishment, and shrinkage depressions will occur, making the fusion line more obvious.
Product Structure
Wall Thickness Variation: Uneven product wall thickness is one of the common reasons for the formation of fusion lines. In the area with a thicker wall thickness, the melt flow speed is relatively slow, while in the area with a thinner wall thickness, the melt flow speed is faster. When the melt from different wall thickness areas meets, it is easy to form fusion lines.
Shape Complexity: The more complex the product shape is, the more complex the flow path of the melt in the cavity will be. The melt needs to go through multiple turns, branches, etc. to fill the entire cavity. During these processes, the melt is likely to form fusion lines at the confluence points of different flow paths.
