PA12, also known as nylon 12, is a type of polyamide 12 and belongs to thermoplastic engineering plastics.
PA12 is formed by the polycondensation of laurolactam and is a linear high - molecular polymer. Its molecular chain contains repeating amide groups (-CONH-), and this structure endows it with numerous unique properties.
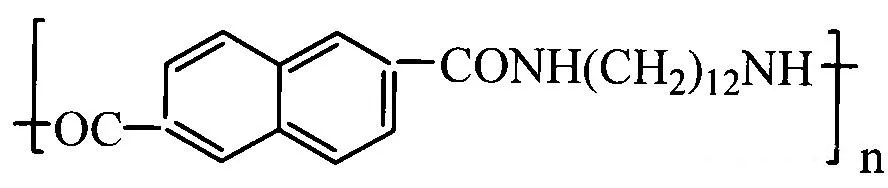
PA12 has outstanding cold - resistance. It can maintain good flexibility and mechanical properties in extremely cold environments. For example, in a - 40℃ low - temperature environment, PA12 products still remain elastic and are not prone to brittle fracture, showing excellent performance in outdoor applications in cold regions.
It has good resistance to many chemical substances and can withstand the erosion of oils, fats, weak acids, and weak alkalis. Take the automotive fuel system as an example. PA12 fuel pipes can be in long - term contact with fuel without being corroded, ensuring the safe and stable operation of the fuel system.
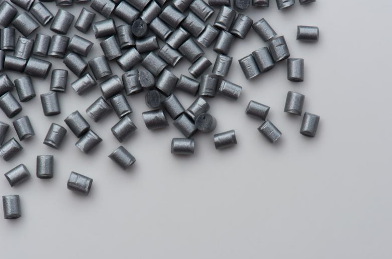
During molding and processing, PA12 has excellent fluidity and can easily fill the mold cavity, enabling the production of products with complex shapes. This characteristic makes PA12 suitable for various processing methods such as injection molding and extrusion molding, improving production efficiency and product precision.
波音彩票PA12 has a relatively low density, being lighter than common engineering plastics such as PA66 and PBT. This is of great significance for reducing the weight of products and lowering costs. In the aerospace and automotive manufacturing industries, the use of PA12 materials can effectively reduce the weight of components and improve energy utilization efficiency.
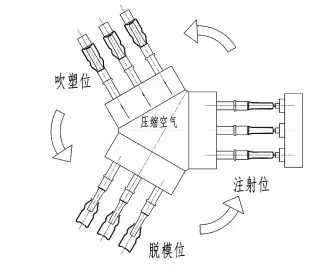
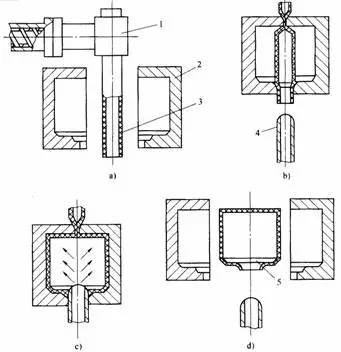
PA12 has relatively high hardness and wear resistance and can withstand long - term friction. For example, in textile machinery, gears and bearings made of PA12 can still maintain good wear resistance under high - speed operation and frequent friction, extending the service life of the equipment.
It is used to manufacture automotive fuel pipes, brake system pipelines, air filter housings, engine hoods, and other components. PA12 fuel pipes have good oil - resistance and anti - permeability, which can effectively prevent fuel leakage and improve the safety and reliability of automobiles.
It can be used to produce insulation layers of wires and cables, outer shells of electronic components, connectors, etc. The insulation layer made of PA12 has good electrical insulation and environmental resistance, protecting wires and cables to operate safely in complex electrical environments.
In the aerospace field, PA12 is used to manufacture some non - critical structural parts, interior parts, and pipeline systems. Its low density and good performance can meet the requirements for material lightweighting and reliability in this field.
PA12 has good biocompatibility and can be used to manufacture outer shells of medical devices, medical catheters, syringe components, etc. For example, PA12 medical catheters are soft and corrosion - resistant, meeting the requirements for use in medical procedures.
In the sporting goods industry, PA12 is often used to manufacture skis, bicycle components, rackets, etc. It can provide good strength, toughness, and wear resistance for sporting goods, improving product performance and service life.
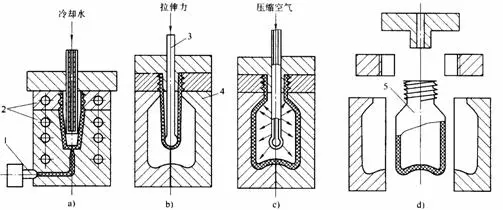
It is one of the commonly used processing methods for PA12. PA12 pellets are heated to a molten state and injected into the mold cavity under high pressure. After cooling and solidification, the product is obtained. This method features high production efficiency and high product precision and can form complex shapes.
It is used to produce continuous - shaped products such as pipes and profiles. PA12 pellets are added to an extruder, heated, and made molten by the rotation of a screw, and then extruded from the die head and cooled and shaped. The products produced by extrusion molding have good dimensional stability and surface quality.
It is mainly used to manufacture hollow products such as plastic bottles and fuel tanks. The molten PA12 material is made into a parison, placed in a mold, and then compressed air is blown in to make it expand and fit the inner wall of the mold. After cooling, a hollow product is obtained.
These also include thermoforming, rotational molding, etc. Thermoforming is to heat a PA12 sheet to a softened state and form it through a mold; rotational molding is to put PA12 powder into a mold, and the mold rotates to make the powder evenly distributed and melt under heat to form a product.
As a thermoplastic engineering plastic with excellent performance, PA12, with its diverse properties given by its unique chemical structure, is applied in a wide range of fields and is compatible with various processing methods to meet different production requirements.
